Huntsman opereert in de Botlek twee fabrieken voor methyleendifenyldi-iso-cyanaat (MDI). Eén van de fabrieken had een bijzondere stop omdat naast het gebruikelijke onderhoud en een aantal aanpassingen aan de fabriek, een volledig nieuw besturingssysteem is geïmplementeerd. Hierbij is een andere besturingsstrategie, waarbij de operator centraal staat, toegepast.
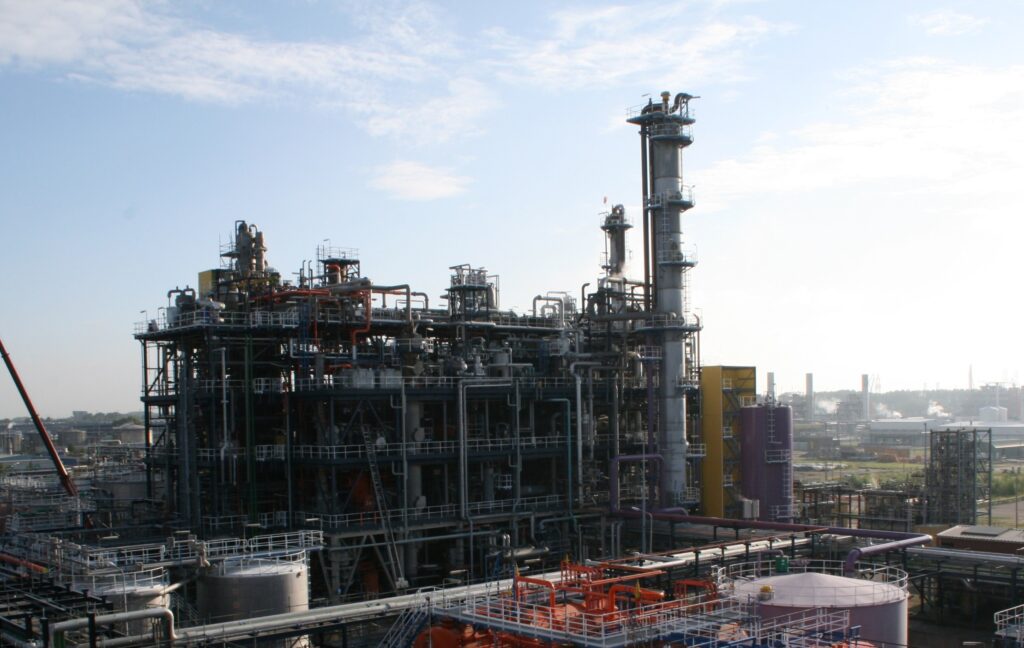
‘Het was een enorme investering waarbij het systeem is vernieuwd in een zeer korte periode, namelijk tijdens een reguliere onderhoudsstop. Dus met het risico op productieverlies wanneer de migratie niet geheel volgens planning zou gaan’, aldus Nanneke de Wolff, Process Excellence Manager Huntsman
Ontwerp besturingsstrategie
Huntsman wilde echter geen één-op-één vervanging van het bestaande systeem. Het bedrijf heeft de migratie aangegrepen om een moderne, state-of-the-art-procesbesturing te installeren, die bijdraagt aan een betere performance van de fabriek. Een van de veranderingen is een nieuwe besturingsstrategie waarin de operator een grotere rol speelt. De Wolff: ‘Een van onze eisen was dat het systeem moest sturen op kennis van operators, en ingericht moest zijn om de operator dienstbaar te zijn en hen te helpen. Het moest niet alleen ingericht zijn om het proces te controleren en te besturen.’
In de nieuwe situatie heeft de operator meer invloed op de fabriek, waarbij de operator zelf keuzes kan maken en heeft meer verantwoordelijkheden en heeft, naast acteren op zaken die mis gaan, nu ook de mogelijkheid om te sturen op KPI’s. Daarvoor was veel aandacht nodig bij het trainen van de operators voor het gebruik van het nieuwe systeem. Hiervoor is een trainingssysteem met een volledige fabriekssimulatie (Digital Twin) gemaakt. Naast deze nieuwe besturingsstrategie, konden nu belangrijke zaken als veiligheid, kennis, controle en de toekomst mee worden genomen. Al deze eisen werden vastgelegd in een visiedocument met een helder omschreven doel.
Eén van de grote uitdagingen lag in het modelleren van de fysische modellen van de processen in de fabriek. Deze dienen zo dicht mogelijk tegen de werkelijkheid aan te liggen. Operators kunnen nu het verschil niet zien of zij met de virtuele fabriek werken of met de werkelijke fabriek. Dat geeft ook mogelijkheden om situaties te trainen zonder dat mens en milieu belast worden, b.vc. een situatie waarbij gevaarlijke stoffen vrij komen.
Naast het voordeel van het trainen van operators bleek ook al snel dat nieuwe functionaliteit getest kan worden op de Digital Twin zonder risico op calamiteiten, productie stops en grondstoffen verlies. En daarmee kunnen nu ook nieuwe scenario’s ten behoeve van proces optimalisatie uitgevoerd worden. Pas als blijkt dat deze toegevoegde waarde leveren kunnen ze na het testen met minimale impact in de echte fabriek doorgevoerd worden.
Voor de stop zijn de operators getraind om te werken met het nieuwe systeem. Met het operator-trainingssysteem hebben de operators verschillende scenario’s getraind met de nieuwe besturingsinterface, bijvoorbeeld de opstart.
Brisq heeft in dit project de besturingsstrategie ontworpen. Wil je van gedachten wisselen over het gebruik van simulatie voor het ontwerp van je besturing, neem dan contact met ons op.